Optimizing Your Welding WPS: Strategies for Improved Efficiency and Performance
Optimizing Your Welding WPS: Strategies for Improved Efficiency and Performance
Blog Article
Opening the Power of Welding WPS: Methods for Efficiency and Safety And Security in Construction
In the realm of fabrication, Welding Procedure Requirements (WPS) stand as the backbone of welding operations, determining the essential steps for achieving both efficiency and safety in the construction process. Comprehending the complexities of WPS is vital to utilizing its full possibility, yet several companies have a hard time to unlock the true power that lies within these records (welding WPS). By diving into the techniques that enhance welding WPS, a world of boosted performance and enhanced security waits for those prepared to explore the nuances of this essential aspect of fabrication

Significance of Welding WPS
The value of Welding Procedure Requirements (WPS) in the manufacture sector can not be overemphasized. WPS function as an essential roadmap that lays out the needed steps to guarantee welds are performed regularly and properly. By specifying important specifications such as welding processes, materials, joint designs, preheat temperatures, interpass temperature levels, filler steels, and post-weld warm treatment needs, WPS give a standard method to welding that improves effectiveness, high quality, and security in fabrication procedures.
Adherence to WPS helps in attaining uniformity in weld top quality, decreasing the likelihood of issues or structural failings. This standardization also helps with conformity with industry policies and codes, ensuring that fabricated frameworks meet the called for safety standards. Additionally, WPS documents allows welders to duplicate successful welding treatments, bring about regular results across various projects.
Essentially, the meticulous development and strict adherence to Welding Treatment Specifications are critical for upholding the stability of welded frameworks, securing against potential threats, and supporting the credibility of construction business for delivering top quality product or services.
Crucial Element of Welding WPS
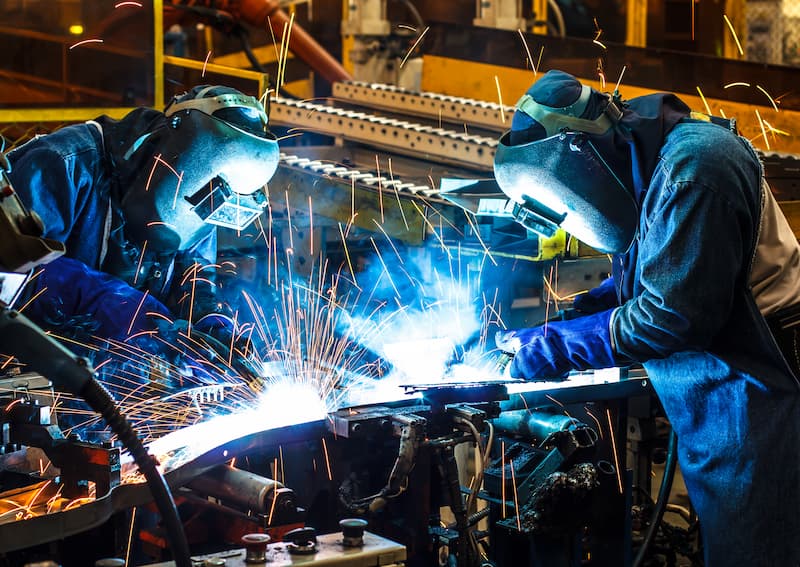
Enhancing Efficiency With WPS
When optimizing welding procedures, leveraging the vital aspects laid out in Welding Procedure Specs (WPS) comes to be important for taking full advantage of and enhancing processes efficiency. One means to boost performance with WPS is by meticulously selecting the appropriate welding criteria.
Moreover, proper training and qualification of welders in understanding and carrying out WPS can additionally improve effectiveness. Guaranteeing that all staff member are skilled in analyzing and executing the WPS properly can rework and minimize errors, conserving both time and resources. Frequently examining and upgrading the WPS to include any kind of lessons found out or technological advancements can likewise add to efficiency renovations in welding operations. By embracing the guidelines set forth in the WPS and continuously looking for ways to maximize processes, makers can accomplish higher performance levels and premium outcome.
Ensuring Safety And Security in Fabrication
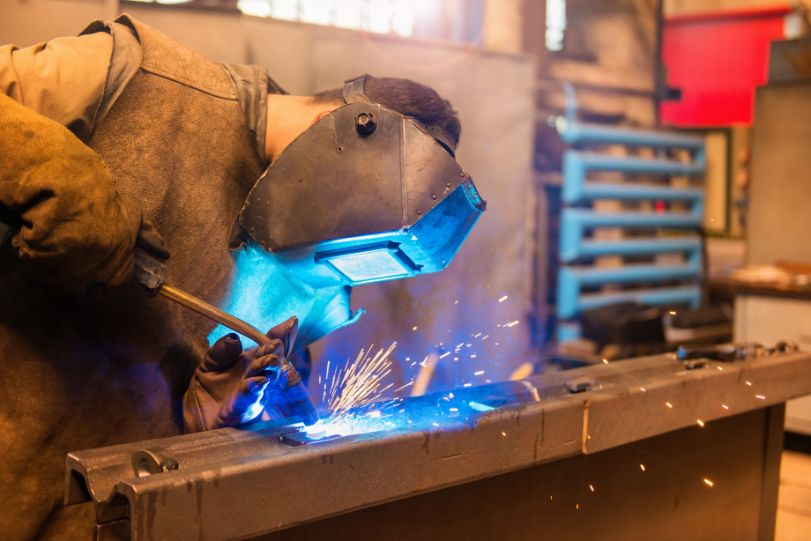
Security methods in construction play a pivotal function in safeguarding workers and maximizing functional procedures. Ensuring security in manufacture includes a multifaceted strategy that incorporates various facets of the welding process. One essential aspect is the arrangement of personal protective tools (PPE) tailored to the certain hazards present in the manufacture environment. Welders must be geared up with suitable equipment such as helmets, gloves, and protective clothing to alleviate dangers related to welding activities.
In addition, adherence to appropriate air flow and fume removal systems is vital in keeping a healthy and balanced job setting. Welding fumes have unsafe materials that, if inhaled, can present significant health risks. Executing efficient ventilation measures aids to reduce exposure to these harmful fumes, advertising respiratory health and wellness among workers.
Normal devices upkeep and check here examinations are also essential for making certain safety in fabrication. Defective machinery can result in injuries and mishaps, highlighting the value of prompt repair work and routine checks. By focusing on precaution and cultivating a culture of recognition, construction facilities can develop a effective and protected job setting for their workers.
Implementing WPS Ideal Practices
To enhance functional efficiency and make certain top quality outcomes in fabrication processes, integrating Welding Treatment Spec (WPS) best methods is critical. Picking the appropriate welding process, filler material, and preheat temperature defined in the WPS is critical for attaining the preferred weld high quality. Ensuring that qualified welders with the essential accreditations carry out the welding procedures according to the WPS guidelines is important for consistency and reliability.
Verdict
In final thought, welding WPS plays a vital duty in making certain performance and safety in manufacture procedures. By focusing on crucial elements, improving performance, and implementing finest methods, firms can enhance their welding operations. It is vital to prioritize safety steps to avoid crashes and ensure a smooth production procedure. By adhering to these strategies, companies can unlock the complete possibility of welding WPS in their fabrication procedures.
In the world of fabrication, Welding Procedure Specs (WPS) stand as the backbone of welding operations, dictating the required steps for accomplishing both effectiveness and security in the fabrication process. By defining essential criteria such as welding processes, products, joint styles, preheat temperature levels, interpass temperature levels, filler metals, and post-weld heat treatment requirements, WPS provide a standard strategy he has a good point to welding that boosts effectiveness, top quality, and safety in construction processes.
When optimizing welding procedures, leveraging the key aspects detailed in Welding Treatment Requirements (WPS) ends up being necessary for simplifying processes and maximizing efficiency. you could try this out (welding WPS)
Report this page